Fluxul procesului

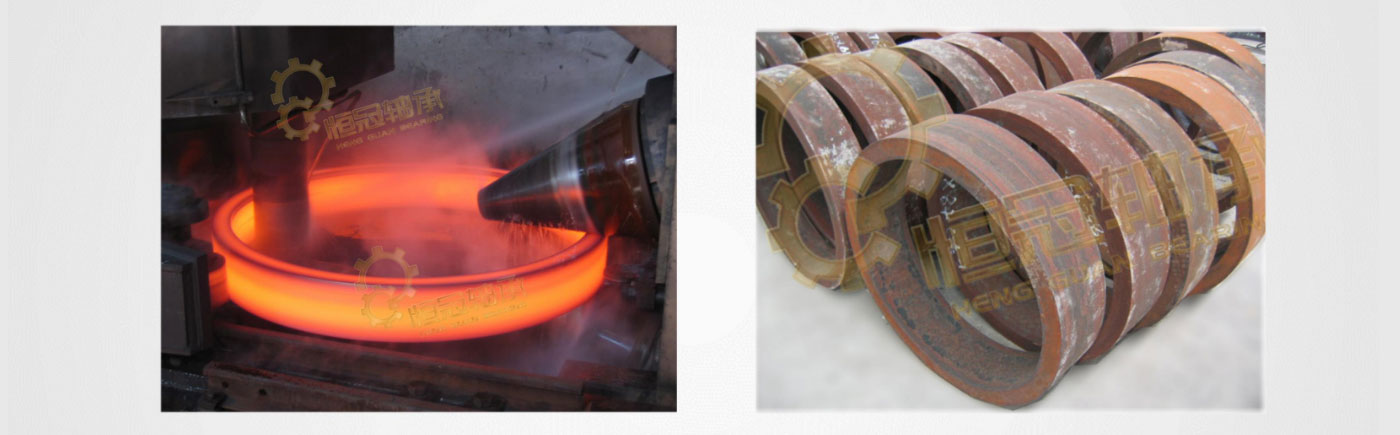
1. Forjare
1. Investigații pe teren, selecție de furnizori de înaltă calitate, eșantionare și testare a materiilor lor prime și eșantionare aleatorie în cooperare ulterioară, pentru a se asigura că materiile prime îndeplinesc standardele naționale, proprietățile mecanice îndeplinesc cerințele de proiectare a produsului.
2. După ce piesele forjate intră în fabrică, inspectorii de calitate inspectează aspectul și măsoară dimensiunea pieselor forjate pentru a se asigura că nu există defecte evidente și marje suficiente pentru prelucrarea produselor finite.

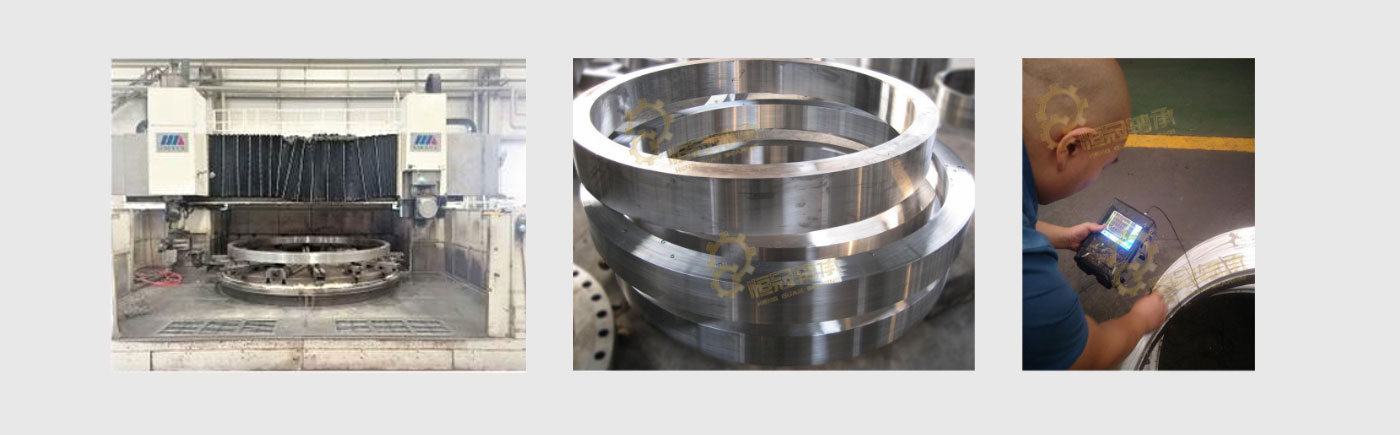
2. strunjire brută
1.Detartrarea strunjirii brute, în funcție de dimensiunea produselor finite, rezervați marje de dimensiuni diferite.
2. Detectarea defectelor cu ultrasunete, piesele forjate după strunjirea brută sunt detectate prin ultrasunete, dacă există defecte ale materialului, cum ar fi suflarea, includerea de zgură, laminarea și așa mai departe.
3. Tratamentul de călire și revenire, conform standardului național sau cerințelor speciale ale clienților, piesele forjate după strunjirea brută sunt călite pentru a îmbunătăți proprietățile mecanice în ansamblu.
4. Testarea durității la călire și revenire, Testarea dacă duritatea globală a forjarilor este calificată în funcție de cerințele de duritate de călire și revenire

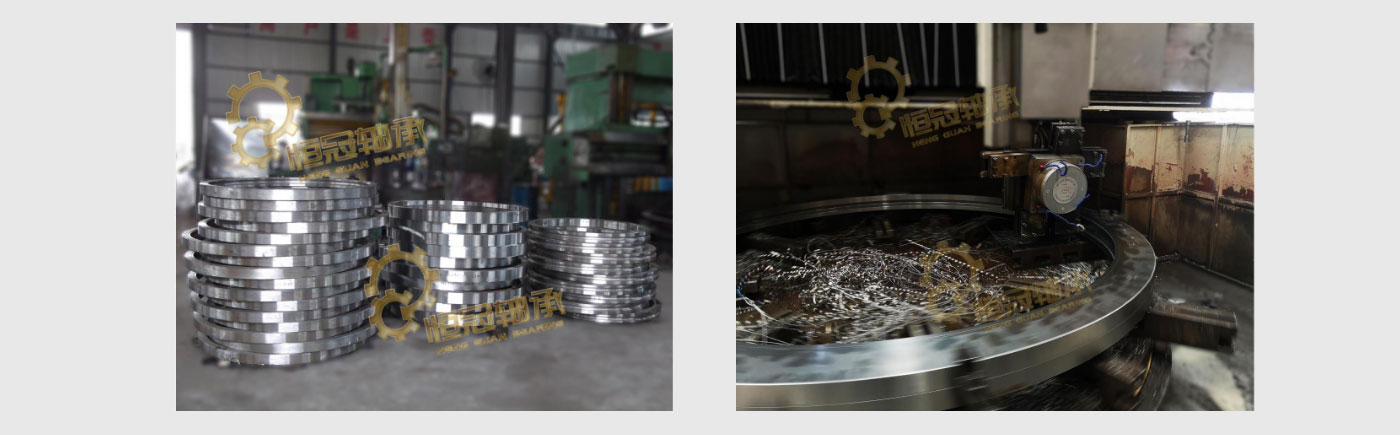
3. Strunjire de precizie înainte de călire
Strunjirea cu precizie a canalului de rulare, rezervând alocație de dimensiuni diferite în funcție de tipul și dimensiunea diferită a structurii canalului de rulare, Garantează că deformarea adăugată de mașină și deformarea de călire pot fi eliminate și, în același timp, asigurând că alocația este cât mai mică posibil.

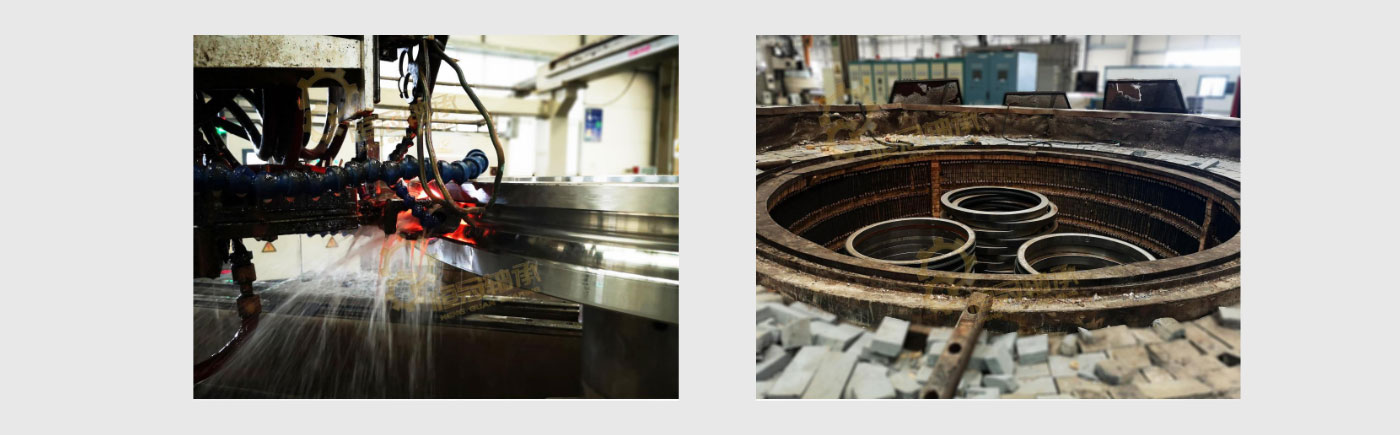
4. Stabilitatea la călire și revenire a căii de rulare
Canalul de rulare este stins prin proces de stingere cu frecvență medie. Duritatea zonei de călire ajunge la HRC55-62, iar adâncimea efectivă nu este mai mică de 3 mm. După călire, calea de rulare este temperată stabil pentru a elimina stresul de călire, pentru a reduce deformarea ulterioară a procesării și pentru a reduce riscul de fisurare a căii de rulare.

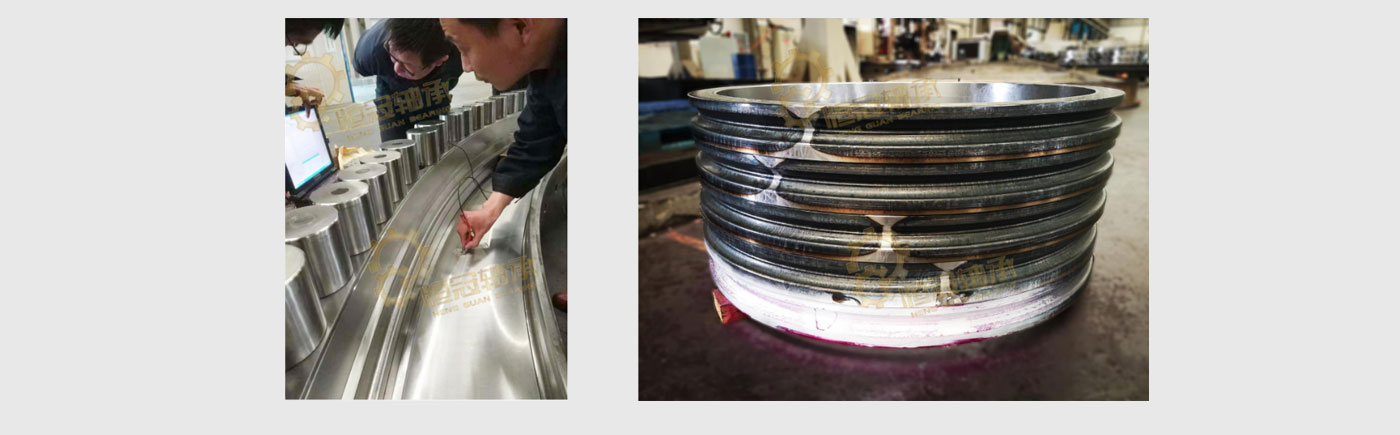
5. Detectarea duritatii
Detectarea durității, adâncimii efective și fisurii în zona stinsă, în special poziția inițială.

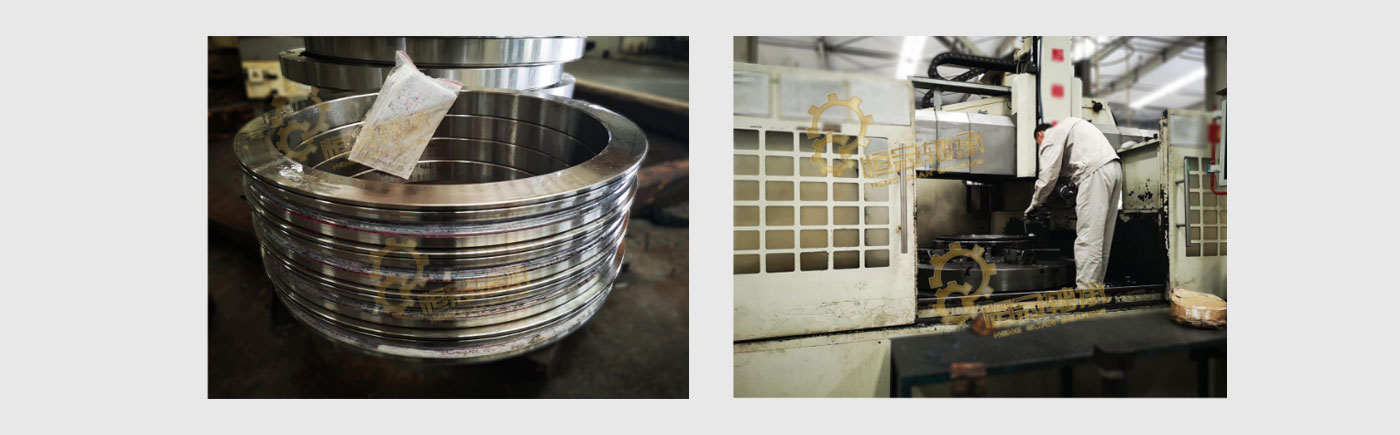
6. Strunjirea semifinisată călită
Nivel de date de prelucrare, furnizarea de date pentru prelucrarea ulterioară a dinților, găurilor etc.

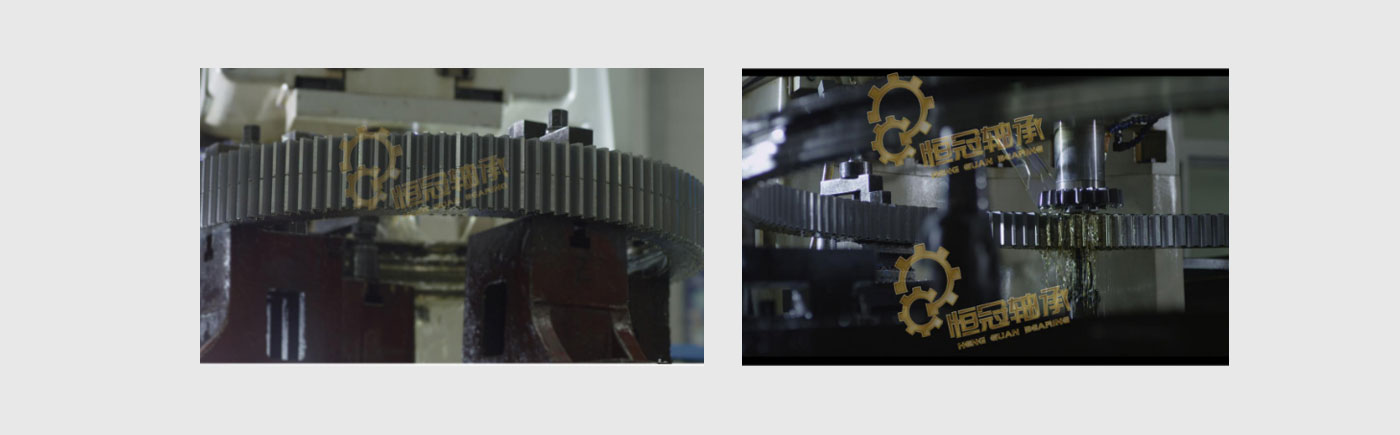
7. Prelucrarea dintilor
În funcție de diferitele forme de dinte, pot fi selectate metode de prelucrare precum modelarea, frezarea și frezarea. Nivelul de precizie poate atinge 7-10 grade. Dacă este necesară o precizie mai mare, șlefuirea poate îndeplini 4-6 grade.

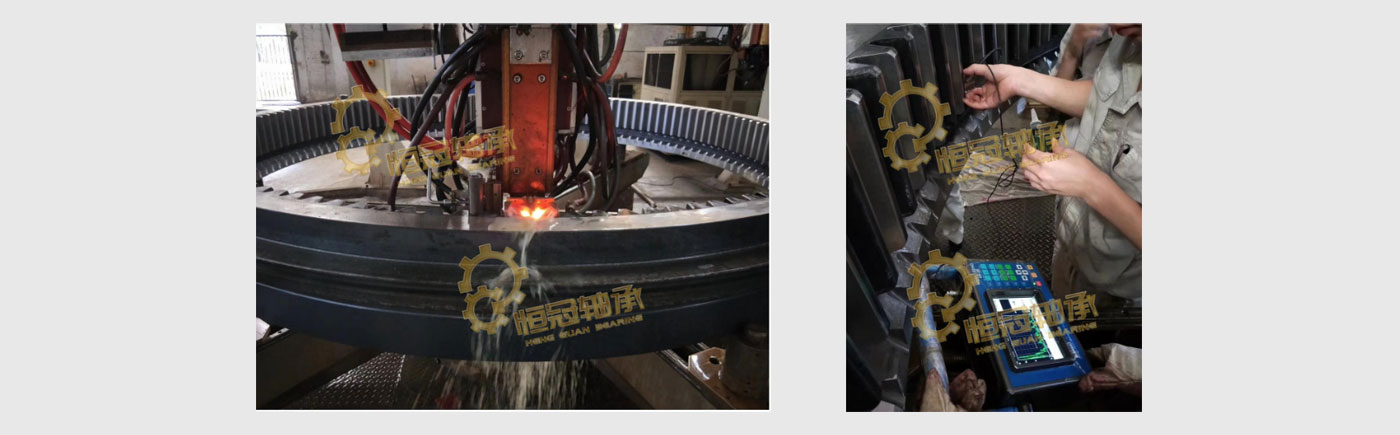
8. Întărirea, stabilitatea călirii și testarea dinților
Pentru a îndeplini rezistența și durata de viață a dinților, se efectuează călirea de înaltă frecvență pe suprafața, rădăcina și vârful dintelui în funcție de diferite cerințe. Duritatea poate îndeplini HRC 40-55, iar adâncimea poate atinge 1,5 mm. Stabilizarea călirii după călire, stresul de călire poate fi eliminat, riscul de fisurare al piesei călite poate fi redus, iar duritatea și detectarea fisurilor pot fi efectuate după călire.

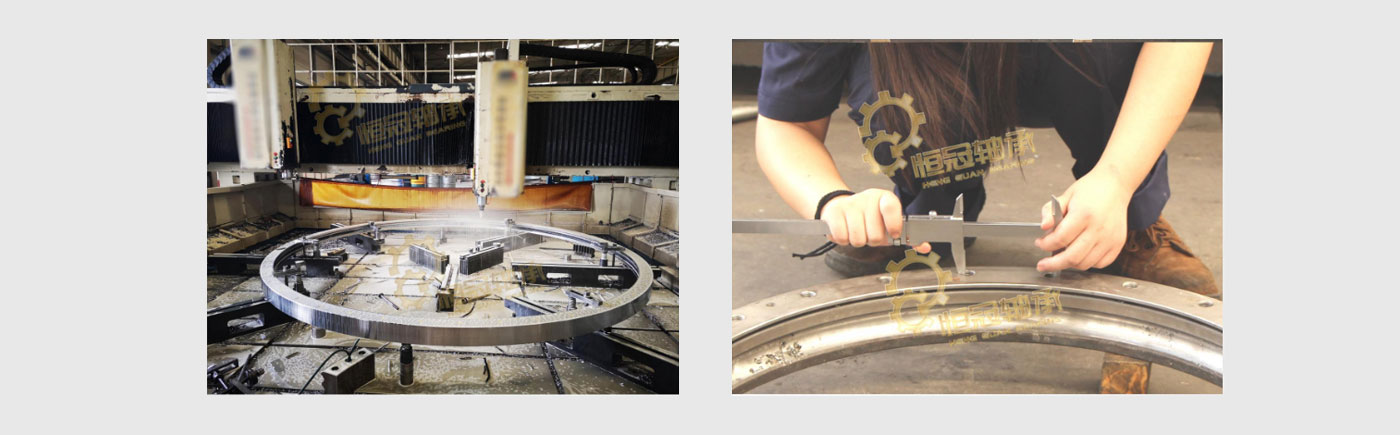
9. Procesarea și detectarea găurilor
Controlați lungimea coardei, grosimea peretelui, deschiderea și alte elemente din procesul de prelucrare și corectați-le la timp. Inspecție pentru filete cu cerințe ridicate de precizie.

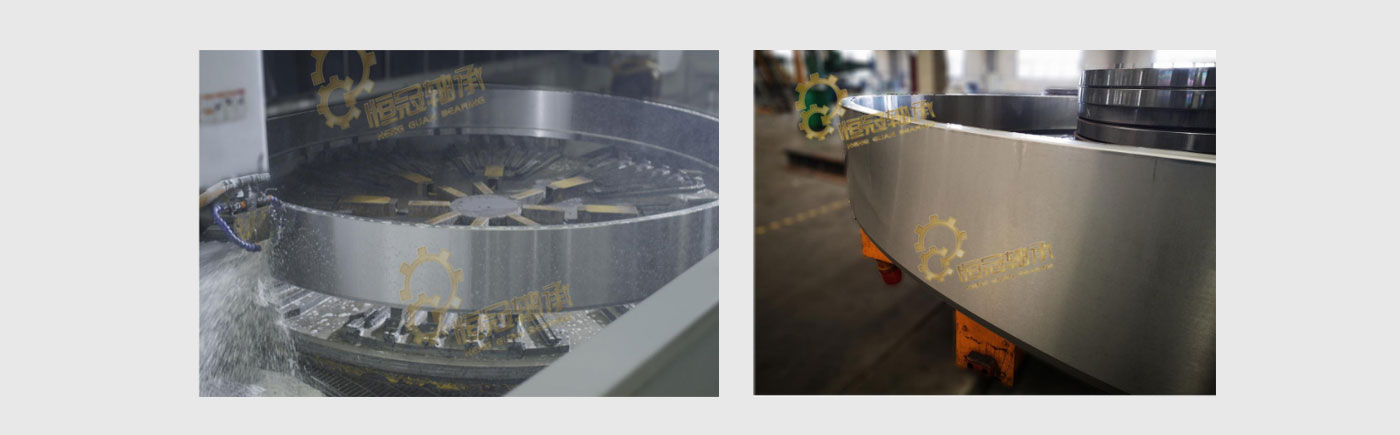
10. Măcinare fină și testare
Pentru produsele de înaltă precizie, șlefuirea precisă este utilizată pentru a controla eficient parametrii elipsei inelului, grosimea peretelui și planeitatea, astfel încât să se asigure că precizia produselor finite îndeplinește cerințele standardelor sau desenelor clienților.

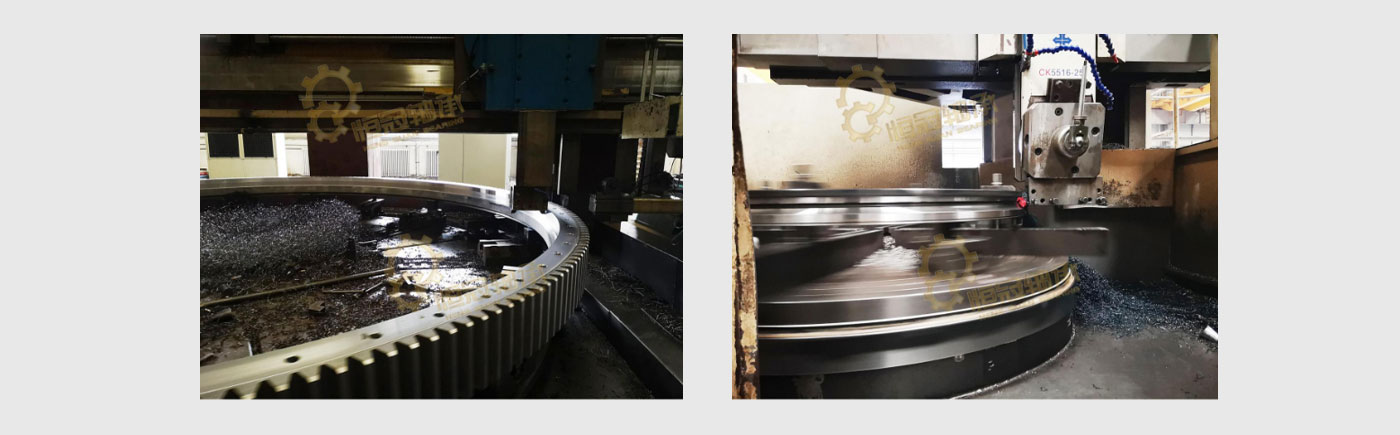
11. Clearance-ul meciului
Măsurarea precisă a dimensiunii piesei, calcularea alocației pentru piese de schimb, în conformitate cu cerințele desenelor pentru a se potrivi cu spațiul liber

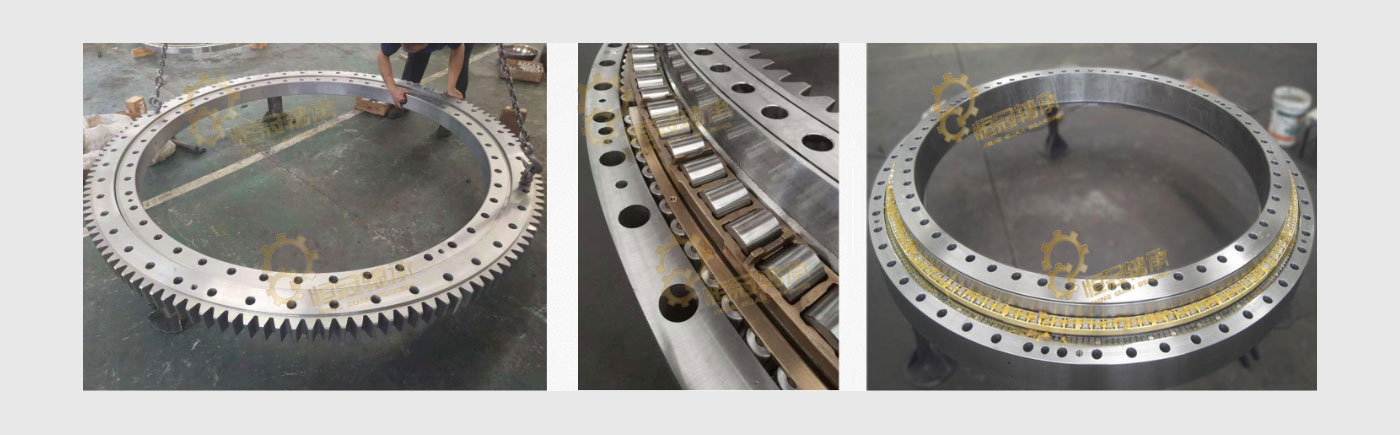
12. Asamblare
Îndepărtați bavurile inelare și curățați. Instalați dimensiunea și numărul corespunzătoare de role, cuști, garnituri și alte accesorii în strictă conformitate cu cerințele desenelor de asamblare. Rotiți pentru a detecta dacă rotația este flexibilă și dacă există vreun zgomot anormal.

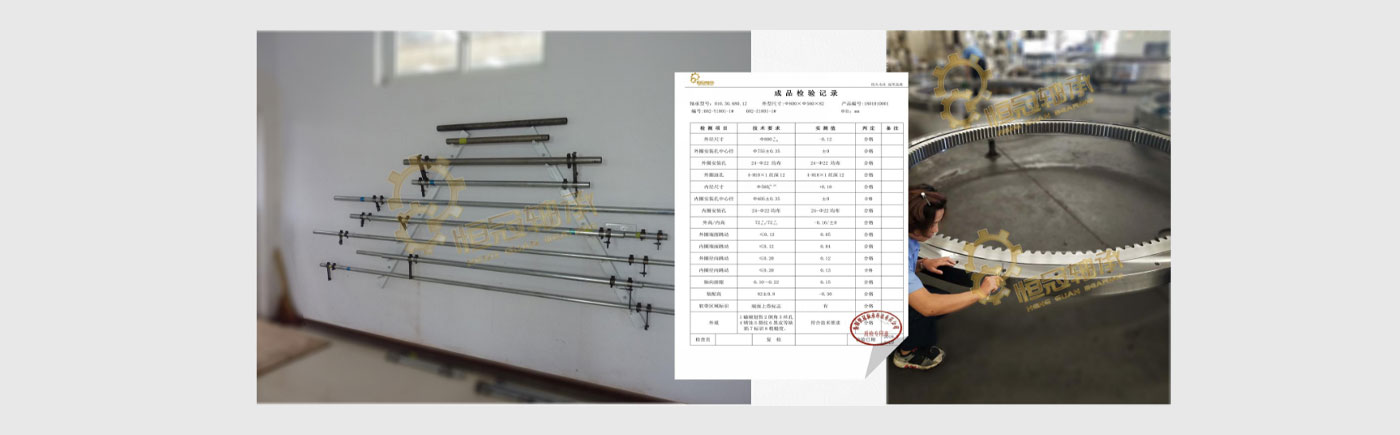
13. Testarea produsului finit
Se finalizează ansamblul, apoi se verifică diferiții indicatori tehnici și se realizează înregistrări detaliate.

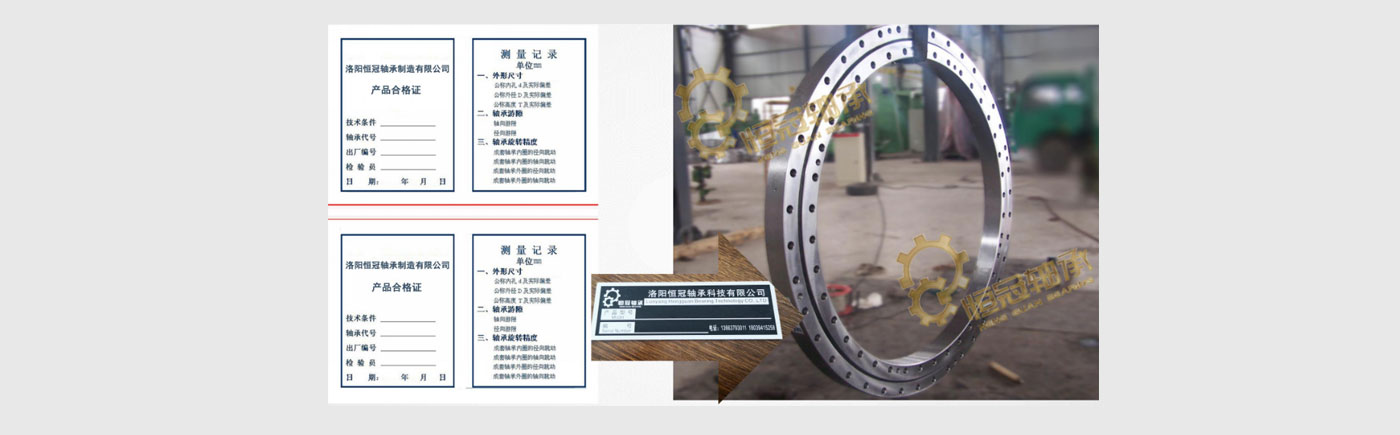
14. Instalarea semnului semnului
Instalați semnul și logo-ul conform cerințelor clientului.

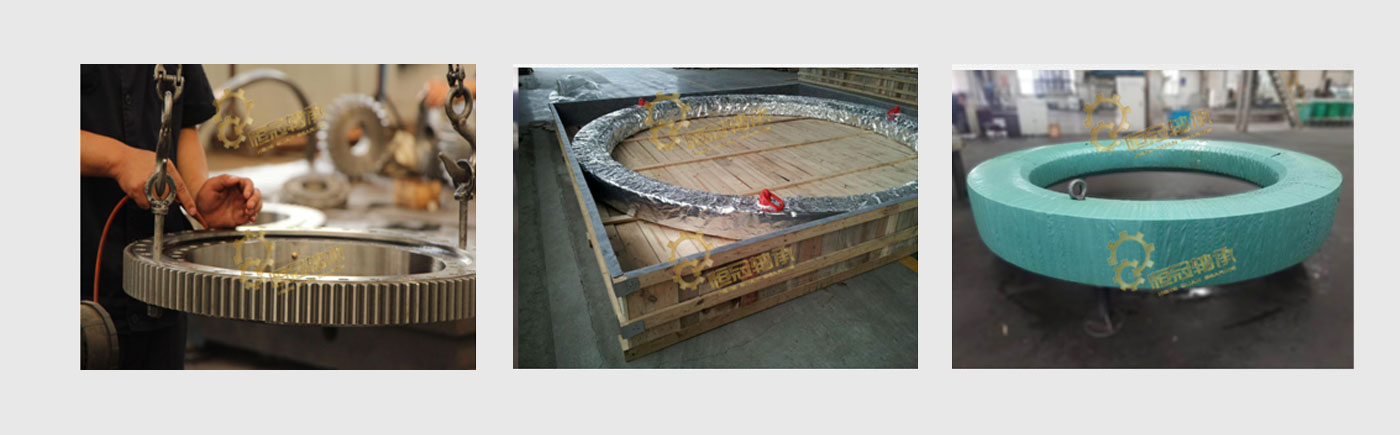
15. Umpleți cu uns și Ambalare
1. Înainte de ambalarea produsului, adăugați unsoare de marcă și tip corespunzătoare conform cerințelor clientului pentru a proteja canalul de deteriorări.
2. Cutiile din lemn de export potrivite pentru transportul maritim sunt folosite pentru a asigura sosirea în siguranță a mărfurilor la diferite distanțe de transport, timpi de depozitare și regiuni.